Understanding CNC Precision Machining
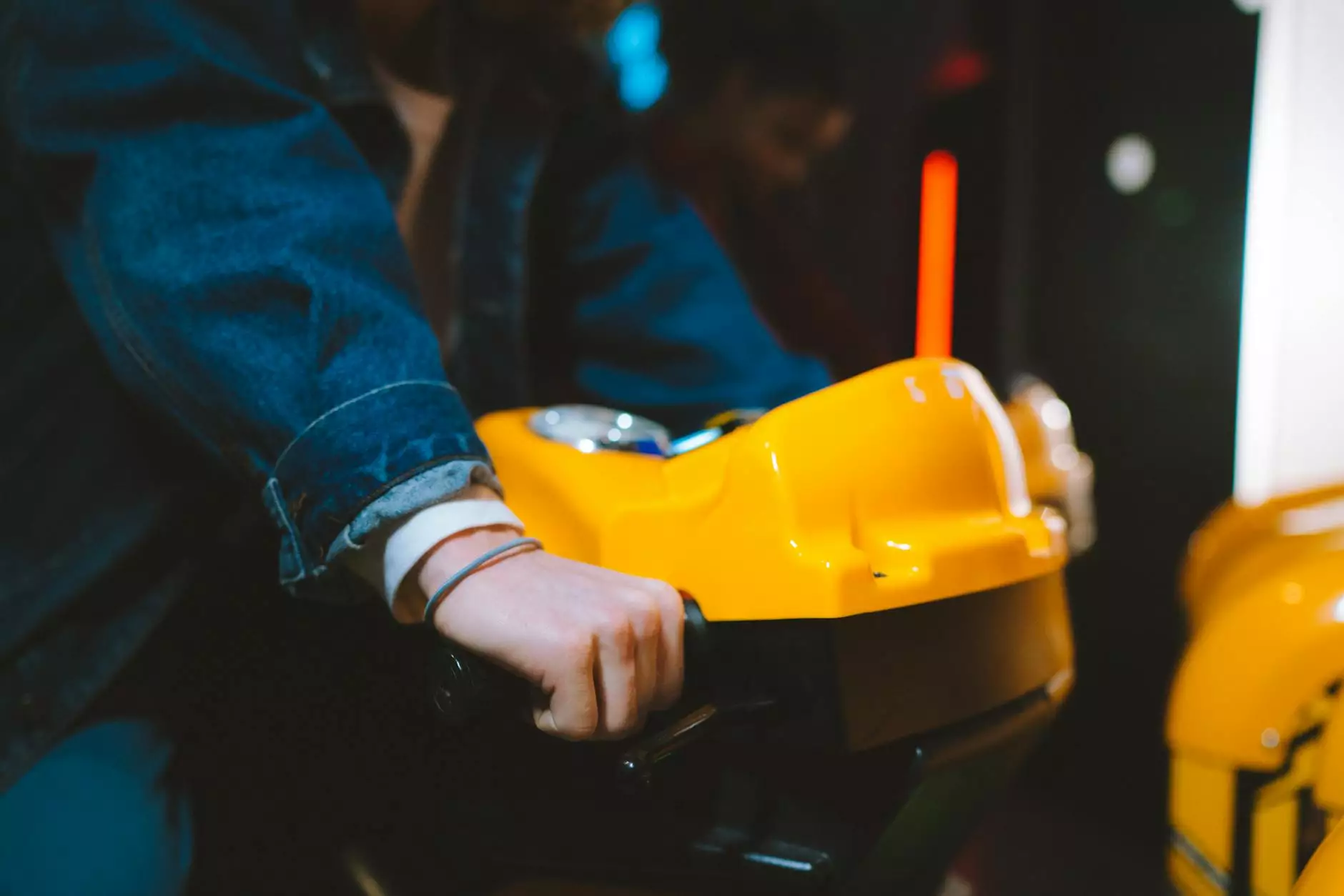
CNC precision machining is a critical element in contemporary manufacturing, particularly in the metal fabrication sector. It integrates advanced technology with skilled craftsmanship, ensuring that products meet stringent specifications and quality standards. This technology employs computer numerical control (CNC) to guide the tools that shape and cut materials with the utmost precision. In this article, we will delve deeper into the world of CNC precision machining, its benefits, applications, and the future of this transformative method.
What is CNC Precision Machining?
CNC precision machining involves the use of computers to control machine tools in the machining process. This technology eliminates the guesswork that traditional machining methods often entail. Instead, it employs a pre-programmed computer software to dictate the movement of factory tools and machinery. The central components of CNC machining include:
- CNC Machines: These machines are programmed with specific instructions for precise cutting and shaping of materials.
- Computer Software: Software applications that create the code required for the CNC machines to perform specific tasks.
- Tooling: Specialized tools designed for various machining operations such as milling, turning, and drilling.
The Benefits of CNC Precision Machining
In the world of metal fabrication, cnc precision machining has introduced numerous benefits that are driving its adoption across industries:
- High Precision and Accuracy: CNC technology ensures extremely precise measurements, resulting in high-quality end products that meet exact specifications.
- Repeatability: Once a machine is programmed, it can produce the same result consistently without deviation, ensuring uniform quality across production batches.
- Efficiency: CNC machines can operate continuously, significantly increasing production speed and efficiency while minimizing human error.
- Versatility: CNC precision machining can work with a variety of materials, including metals, plastics, and wood, making it an adaptable solution for many manufacturing needs.
- Reduced Labor Costs: Automation facilitates a decrease in labor requirements, allowing skilled workers to focus on more complex tasks.
Applications of CNC Precision Machining
The versatility of cnc precision machining makes it suitable for a diverse range of applications across various industries:
- Aerospace: Production of intricate parts that adhere to strict safety and performance standards.
- Automotive: Manufacturing components such as gears, valves, and brackets with a focus on durability and performance.
- Medical: Precise creation of surgical instruments and implants that require high precision and biocompatibility.
- Electronics: Fabrication of parts for devices that demand tiny, complex, and exact components.
- Defense: Production of critical components for military equipment, ensuring reliability under extreme conditions.
How CNC Precision Machining Works
The CNC machining process is a multi-step operation, encompassing several stages from design to final product. The typical workflow includes:
- Design Phase: Engineers create detailed CAD (Computer-Aided Design) drawings or 3D models of the components to be manufactured.
- CNC Programming: The designs are converted into CNC programs using CAM (Computer-Aided Manufacturing) software, generating G-code that directs the CNC machine.
- Setup: The CNC machine is calibrated and set up with the appropriate tools and materials.
- Machining: The CNC machine executes the program, cutting and shaping the material according to specifications.
- Finishing: After machining, parts undergo finishing processes such as sanding, polishing, or coating to achieve the final desired quality and aesthetics.
- Quality Control: Rigorous checks are performed to ensure that every component meets industry standards and client specifications.
The Future of CNC Precision Machining
The future of cnc precision machining is poised for exponential growth and innovation. Key trends shaping this evolution include:
- Integration with AI: Artificial intelligence is being harnessed to enhance CNC operations, leading to smarter machines and quicker adaptation to changes in requirements.
- Additive Manufacturing: The combination of machining with 3D printing technology can streamline production processes and expand design possibilities.
- Increased Automation: Automation continues to rise, with advancements in robotics further improving efficiency and reducing the need for manual intervention.
- Sustainable Practices: Focus is shifting toward minimizing waste and using eco-friendly materials, making CNC precision machining more sustainable.
- Skills Development: Training programs are expanding to equip workers with the skills necessary to operate advanced CNC machinery and adapt to new technologies.
Conclusion
CNC precision machining stands at the forefront of modern manufacturing, providing unparalleled accuracy, efficiency, and versatility. As industries continue to evolve and demand higher-quality products in shorter timeframes, the importance of this technology cannot be overstated. By harnessing the capabilities of CNC machines, businesses like Deep Mould are set to lead the charge into a new era of manufacturing excellence.
Getting Started with CNC Precision Machining
For businesses looking to adopt CNC precision machining, several steps can set the foundation for success:
- Identify Your Needs: Assess your production requirements and determine how CNC machining can meet these needs.
- Choose the Right Equipment: Select machines and tools that match your production scale and types of materials.
- Invest in Training: Providing training for your team can enhance productivity and ensure safety standards are upheld.
- Implement Quality Control Measures: Establish a quality control framework to maintain high standards throughout the manufacturing process.
Final Thoughts
Incorporating cnc precision machining into your business strategy can significantly enhance your production capabilities and competitive edge. By understanding its benefits, applications, and future developments, you will be better equipped to leverage this technology for the growth and success of your enterprise.