Unlocking Potential: A Comprehensive Guide to China Lathe Machine Parts Manufacturers
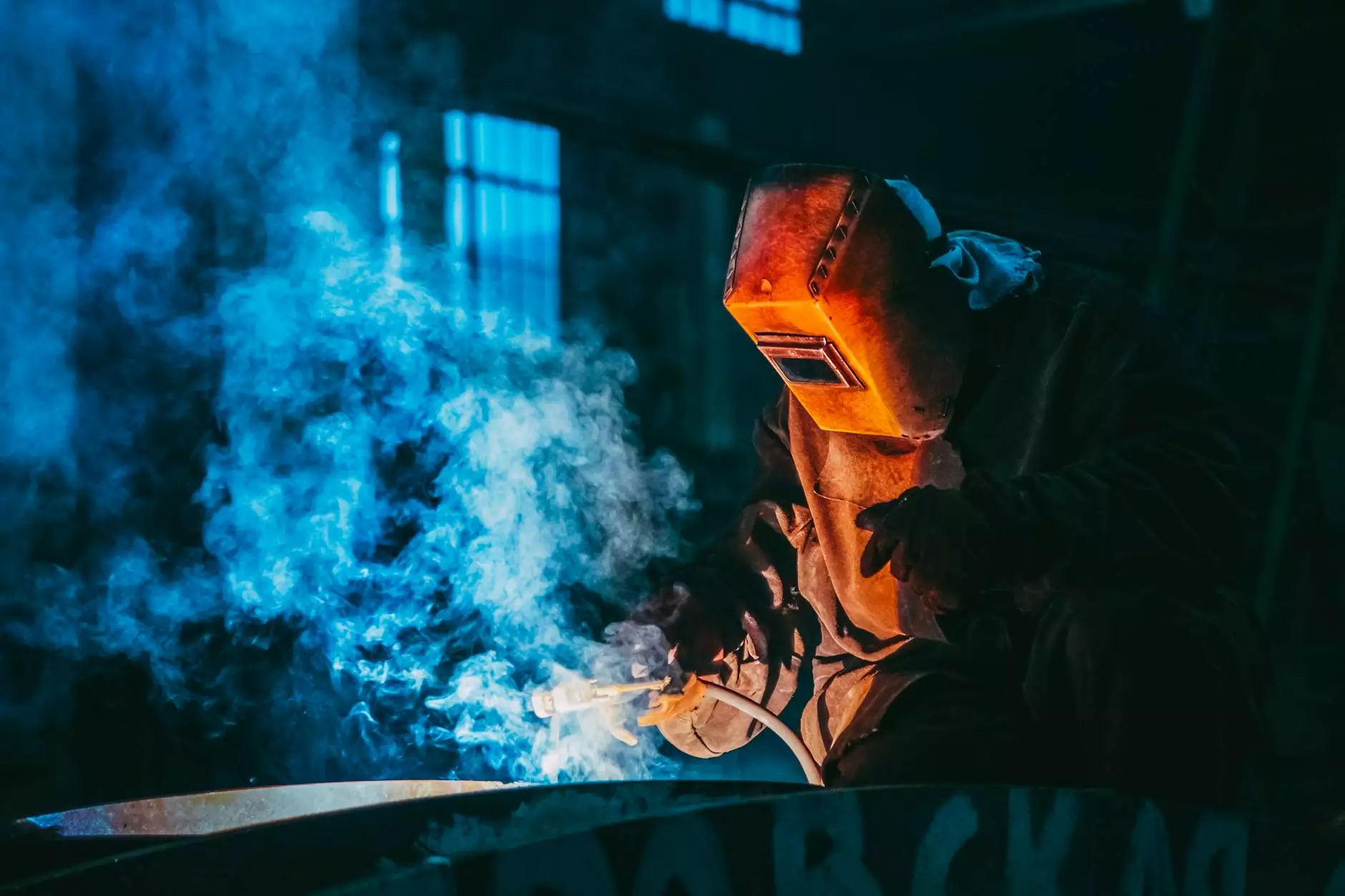
In the ever-evolving landscape of manufacturing, efficiency, cost-effectiveness, and technological advancement are paramount. For businesses in the metal fabrication sector, collaborating with China lathe machine parts manufacturers presents numerous advantages that can significantly enhance operational capabilities. This article delves into the world of lathe machine parts, emphasizing their crucial role in the manufacturing process while elucidating the advantages of sourcing from China.
Understanding Lathe Machines and Their Components
Lathe machines are fundamental tools in the metalworking industry, used primarily to shape materials through rotary motion. The components of a lathe machine include:
- Headstock: Houses the main spindle and motor.
- Tailstock: Provides support and can hold tools or workpieces.
- Bed: The foundation where all components are mounted.
- Carriage: Moves tools into position for cutting.
- Feed mechanism: Controls the advancement of the tool.
Each of these parts plays a vital role in ensuring precision and accuracy in machining operations.
The Importance of Quality Parts
In metal fabrication, the quality of lathe machine parts directly influences productivity and the final products’ quality. Low-quality parts can lead to errors, increased operational downtime, and ultimately, financial losses. Therefore, sourcing high-quality lathe machine parts from China lathe machine parts manufacturers becomes essential for maintaining high operational standards.
Advantages of Partnering with China Lathe Machine Parts Manufacturers
1. Cost-Effectiveness
One of the most compelling reasons to choose Chinese manufacturers is the significant cost savings. Due to lower labor costs and economies of scale, many China lathe machine parts manufacturers can offer competitive prices without compromising on quality. This advantage allows businesses to:
- Reduce production costs.
- Allocate budget towards other critical operational areas.
- Enhance overall profitability.
2. Advanced Technology and Innovation
China is at the forefront of technological advancement in the manufacturing sector. Many manufacturers are adopting the latest technologies in production processes, including:
- Computer Numerical Control (CNC) machining.
- Automation and robotics.
- 3D printing and additive manufacturing.
This integration of advanced technologies ensures that businesses receive products that meet the highest industry standards, providing a competitive edge.
3. Diverse Range of Products
China is home to numerous manufacturers specializing in various lathe machine parts. This diversity allows businesses to find specific parts tailored to their needs. Some of the commonly available components include:
- Chucks and collets for holding tools and workpieces.
- Tool holders designed for specific cutting applications.
- Gears and pulleys that support movement and power transmission.
- Custom-made components tailored to specific machinery.
4. High Quality and Compliance
Many China lathe machine parts manufacturers adhere to global quality standards such as ISO 9001. This compliance ensures that products undergo rigorous testing and quality control measures, resulting in:
- Reduced risk of defects.
- Consistent product quality.
- Increased reliability and performance of machinery.
5. Access to Global Supply Chains
Partnering with Chinese manufacturers provides access to an extensive global supply chain. This allows businesses to:
- Source additional components efficiently.
- Optimize inventory management.
- Ensure timely delivery of products and services.
Navigating Challenges in Sourcing from China
While there are numerous advantages, it’s essential for businesses to navigate potential challenges associated with sourcing from China lathe machine parts manufacturers. Some of the common challenges include:
- Communication Barriers: Differences in language and business practices can lead to misunderstandings.
- Quality Control: It’s crucial to establish stringent quality control to mitigate risks associated with defects.
- Shipping and Logistics: Understanding international shipping regulations is vital for timely delivery.
- Cultural Differences: Being aware of cultural aspects can facilitate smoother negotiations and partnerships.
Strategies for Successful Sourcing
To successfully navigate these challenges, businesses can adopt several strategies:
- Conduct Thorough Research: Investigating manufacturers’ reputations and histories can reveal valuable insights.
- Establish Clear Communication: Utilize professional translation services to avoid language barriers.
- Start with Small Orders: Placing smaller initial orders allows for quality assessment before larger commitments.
- Utilize a Local Agent: Having a local partner in China can simplify negotiations and logistics.
Case Studies: Successful Collaboration with Chinese Manufacturers
Numerous companies have successfully thrived by partnering with China lathe machine parts manufacturers. Here are a couple of examples:
Case Study 1: XYZ Manufacturing Inc.
XYZ Manufacturing Inc., a leading metal fabricator, faced challenges in meeting production demands due to high costs for local parts. After switching to Chinese manufacturers, they not only reduced their costs by 30% but also improved the quality of their lathe parts, resulting in fewer defects and higher customer satisfaction.
Case Study 2: ABC Precision Engineering
ABC Precision Engineering successfully leveraged Chinese suppliers to introduce innovative CNC machine components. By collaborating with technology-forward manufacturers, they increased production efficiency by 40% and gained a notable competitive advantage in the precision engineering sector.
Future Trends in Lathe Machine Manufacturing
The landscape of lathe machine parts manufacturing is continually evolving. Potential future trends include:
- Sustainability: Manufacturers are increasingly focusing on eco-friendly production processes.
- Smart Manufacturing: The integration of IoT and AI technologies to enhance efficiency and quality.
- Customization: A shift towards more personalized parts tailored to specific client needs.
- Global Collaboration: Increased collaboration between manufacturers worldwide to access diverse expertise.
Conclusion
Partnering with China lathe machine parts manufacturers offers a multitude of benefits ranging from cost savings and improved product quality to access to advanced technology and a diverse range of components. By understanding and navigating potential challenges, businesses can successfully leverage these partnerships to enhance their operational capabilities and achieve greater success in the competitive metal fabrication industry.
For manufacturers looking to maximize efficiency and quality, embracing the possibilities offered by Chinese suppliers is not just advantageous but essential in today’s dynamic market landscape. Visit deepmould.net to explore more about how precision parts and innovative solutions can transform your business.