Understanding Silicone Membranes for Vacuum Press Applications
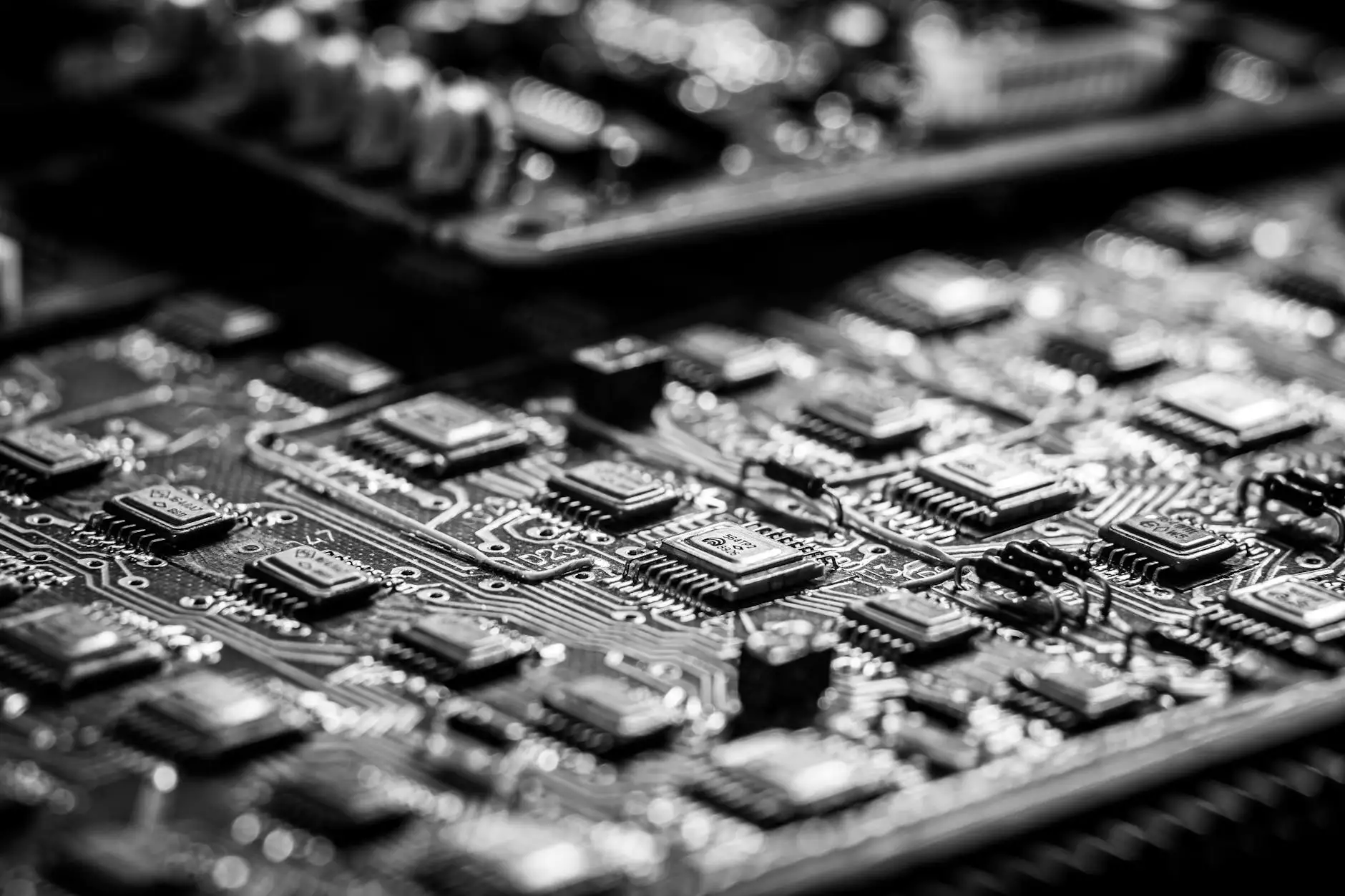
In the realm of manufacturing and processing, silicone membranes for vacuum press systems play a pivotal role. These sturdy yet flexible materials are not just components; they are essential elements that ensure quality, efficiency, and longevity in various industrial applications. This article will delve into the details of silicone membranes, their advantages, applications, and where you can find high-quality options at vacuum-presses.com.
The Role of Silicone Membranes in Vacuum Applications
Silicone membranes are specialized materials used in vacuum presses to create a tight seal between the pressing surface and the material being processed. Their unique properties make them particularly suited for this role. Here’s why:
- High Temperature Resistance: Silicone membranes can withstand significant temperature variations, making them ideal for hot pressing processes.
- Durability: They exhibit excellent durability and resistance to wear and tear, ensuring a longer lifespan compared to other materials.
- Flexibility: The inherent flexibility of silicone allows for an even distribution of pressure, promoting better results in the final product.
Benefits of Using Silicone Membranes
The benefits of utilizing silicone membranes for vacuum press applications are manifold:
1. Enhanced Efficiency
Silicone membranes contribute significantly to the efficiency of vacuum presses. Their ability to maintain optimal sealing ensures that air is effectively evacuated, leading to quicker processing times and improved output quality. By using high-quality silicone membranes, businesses can achieve better material yield and minimize waste.
2. Cost-Effectiveness
Though they may represent a higher initial investment, the durability and longevity of silicone membranes result in lower overall operational costs. Frequent replacements of low-quality membranes can add up, making silicone a financially wise choice in the long run.
3. Versatility in Applications
Silicone membranes are versatile and can be used in various applications beyond traditional vacuum pressing. These include:
- Woodworking - for laminating and veneering processes.
- Composites - ideal for bonding fiberglass and other materials.
- Automotive - used in manufacturing parts through vacuum bagging.
- Electronics - for encapsulating components and creating seals.
Choosing the Right Silicone Membrane
When selecting a silicone membrane for vacuum press, it is essential to consider several factors to ensure optimal performance:
1. Thickness
The thickness of the membrane can significantly affect its performance. Thicker membranes tend to be more durable but may impact flexibility. Consequently, businesses should select a thickness that balances durability and application requirements.
2. Shore Hardness
Silicone membranes come in various shore hardness levels. Softer membranes provide more flexibility, while harder ones offer enhanced durability. Depending on the application, a specific shore hardness may be more suitable.
3. Temperature Range
Different applications may require different temperature tolerances. Always check the specifications of the silicone membrane to ensure it meets the temperature requirements of your processes.
4. Chemical Resistance
If your application involves exposure to chemicals, it is crucial to select a silicone membrane that provides adequate chemical resistance to prevent degradation and ensure longevity.
Maintenance and Care of Silicone Membranes
To extend the lifespan and efficiency of your silicone membranes, it's vital to implement proper maintenance practices:
1. Regular Inspection
Regularly inspect your membranes for any signs of wear or damage. Early detection of issues can prevent significant operational disruptions.
2. Cleaning
Keeping your silicone membranes clean is essential. Use warm water and a mild detergent to remove any adhesive residues or contaminants that may affect performance.
3. Storage
Store silicone membranes in a cool, dry place away from direct sunlight and extreme temperatures to avoid deformation or degradation when not in use.
Conclusion
In conclusion, silicone membranes for vacuum presses are indispensable components in various manufacturing sectors. Their combination of durability, flexibility, and resistance to heat and chemicals makes them a top choice for businesses looking to enhance their production processes. By carefully selecting the right membrane and adhering to proper maintenance practices, you can ensure optimal performance and longevity.
For high-quality membranes and other vacuum system parts, explore our offerings at vacuum-presses.com. Investing in the right equipment is crucial for your business's success, and choosing the right silicone membranes is a step towards achieving operational excellence.
Frequently Asked Questions (FAQs)
1. What is the lifespan of a silicone membrane?
The lifespan of a silicone membrane largely depends on usage, maintenance, and the specific conditions of the application. However, with proper care, they can last several years.
2. Can I use silicone membranes in high-pressure applications?
While silicone membranes are designed to handle vacuum applications effectively, their ability to withstand pressure depends on the specific product. Always check with the supplier for compatibility.
3. Are silicone membranes safe for food-grade applications?
Food-grade silicone membranes are available and can be used in applications involving food processing. Ensure that the membranes you're purchasing are certified food-safe.
4. Where can I buy silicone membranes for vacuum presses?
You can find a wide selection of silicone membranes and other vacuum system parts at vacuum-presses.com, where quality meets reliability.
5. How do I know if I need a silicone or rubber membrane?
The choice between silicone and rubber membranes largely depends on the specific requirements of your application, including temperature resistance, flexibility, and cost. Generally, silicone is favored for its higher temperature and chemical resistance.